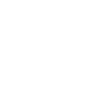
Powerful Naval Architecture Software
Create initial hull designs and assess stability of all types of existing marine vessels. Use this complete set of integrated naval architecture tools to visualize and optimize vessel designs.
What is MAXSURF?
Maxsurf is naval architecture software ideal for the design of marine vessels. Maxsurf includes capabilities for hull modeling, stability, motions and resistance prediction, structural modeling, structural analysis, and export to vessel detailing. Maxsurf operates from a single parametric 3D model in order to ensure smooth communication and coordination across various involved in the project.
Assess Vessel Compliance
Ensure compliance with international stability criteria and balance vessel performance requirements using integrated analysis tools. Perform a range of analyses including intact and damaged stability, resistance and motions prediction, and structural analysis.
Model Marine Vessels
Create complex 3D hull forms for any type of vessel using wizards and interactive sketch tools. Systematically explore design alternatives by making measured changes to models with easy-to-use tools. Apply transformations to increase the productivity of the initial hull design process.
Optimize Vessel Design
Perform faster hull form variation and analysis with team-based concurrent modeling on a common 3D parametric model. Easily visualize and assess design alternatives within a consistent graphical environment with smooth data flow.
Maximize Vessel Performance
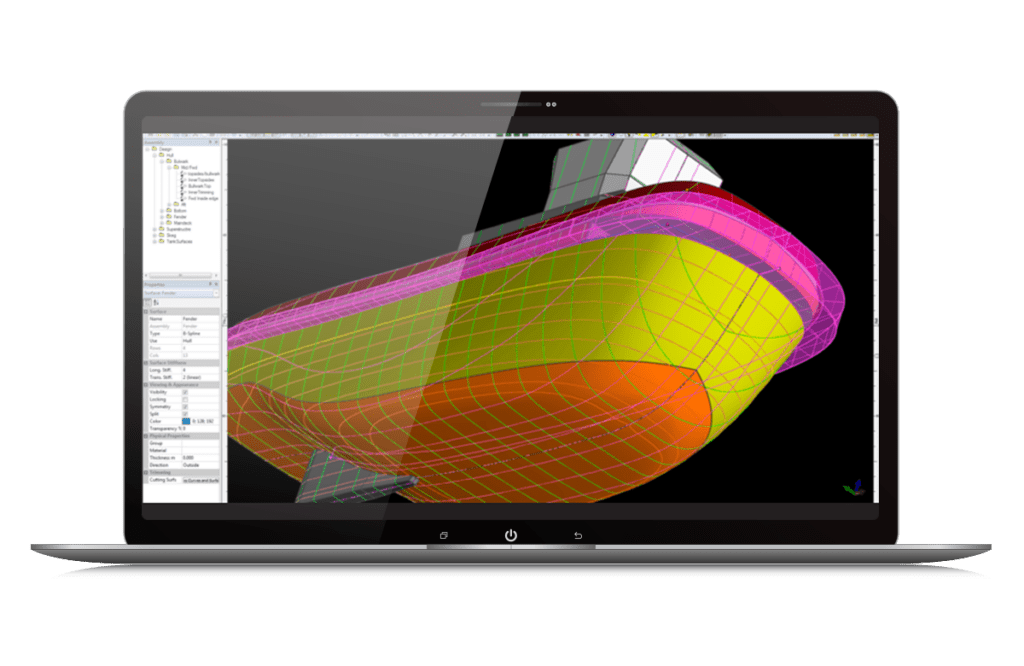
Maxsurf
- Model complex vessels using dynamically trimmed 3D NURB surfaces
- Flexible data import, mesh modeling, and automatic curve and surface fitting
- Design power, sail, commercial, and naval vessels made from steel, aluminum, wood, or composite materials
- Probabilistic damage stability
- Radiation diffraction panel method motions prediction
- Dynamic, time domain, and structural analysis
FAQs
Maxsurf offers comprehensive capabilities for the design of all types of marine vessels. Maxsurf includes capabilities for hull modeling, stability, motions and resistance prediction, structural modeling, structural analysis, and export to vessel detailing. Maxsurf applications operate from a single parametric 3D model that facilitates smooth communication and coordination among different team members and design activities.
Maxsurf is based on industry-standard NURB surface modeling. It reads and writes DGN, 3DM, IGES, and DXF files, which facilitate a smooth data transfer with MicroStation, Rhino, AutoCAD, ShipConstructor, and SolidWorks. It also features copy and paste to and from Microsoft Excel, and a full automation interface, compatible with Microsoft Excel and Microsoft Word, that allows macros to be used to control Maxsurf for optimization studies or customized calculation and reporting.
The price of Maxsurf varies per region. While there are various types of licensing available, a common choice is the 12-month practitioner license offered through Bentley’s eStore. When you purchase through the eStore you get a Virtuoso Subscription which means you get both the software AND the training, expert services, and custom mentoring you need to get started quickly.
Processor
CPU: Pentium 4 or higher
Operating System
Windows 8/8.1, 10, 11
Memory
RAM: Minimum 2 GB–SACS performance is dependent on model size and resources available
Hard Disk
Minimum 10 GB partition for SACS installation recommended
Display
Graphics card with a chipset that supports Open GL
Network
A network connection is required. 100 Base-T or greater local area ethernet network TCP/IP network protocol is supported
For the most up-to-date system requirements, visit Bentley Communities.